Hundreds of new ceramic materials with extreme heat and electronic tolerances have been discovered by a predictive computational method.
Harder than steel and stable in chemically corrosive environments, the materials – some of which have now been produced – were found using a method developed by materials scientists at Duke University in North Carolina. They could form the basis of new wear- and corrosion-resistant coatings, thermoelectrics, batteries, catalysts and radiation-resistant devices, the team said. One potential use could be for heat-impervious electronics in the aerospace industry. SiCPU products
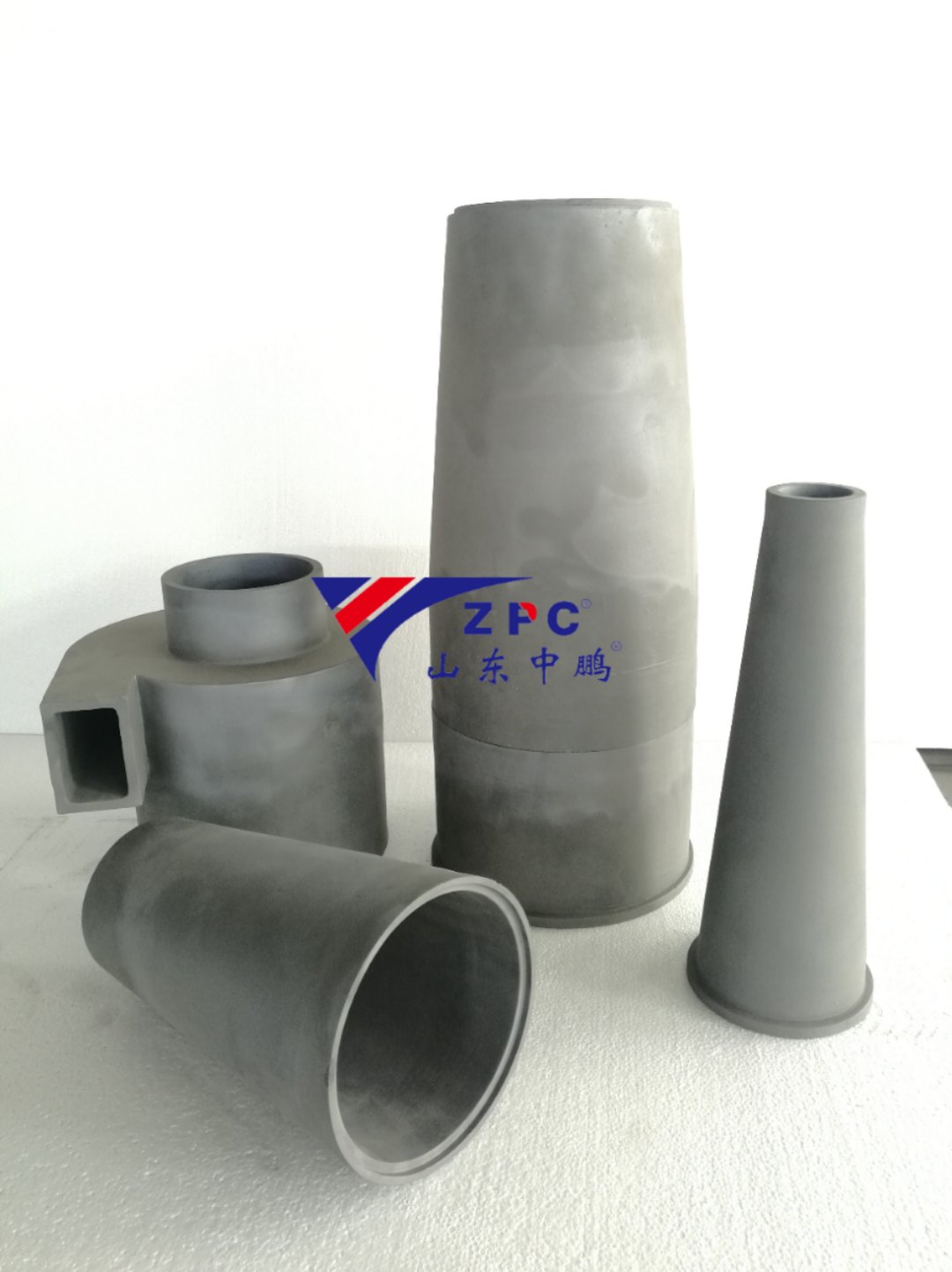
The ceramic materials, which could enable devices to function at lava-like temperatures (800-1,200ºC), were made using transition metals, carbonitrides or borides. They were discovered through a new computational method called the Disordered Enthalpy-Entropy Descriptor (Deed). In its first demonstration, the program predicted the ‘synthesizability’ of 900 new formulations of high-performance materials, 17 of which were then produced and tested in laboratories.
“The capability of rapidly discovering synthesizable compositions will allow researchers to focus on optimising their industry-disrupting properties,” said Professor Stefano Curtarolo.
The researchers maintain a large database of material properties, which is connected to online tools for material optimisation. That information allows algorithms to accurately predict the properties of unexplored mixtures of ingredients, without having to simulate the complexities of atomic dynamics or make them in the laboratory.
For several years, the Curtarolo group has been developing predictive powers for high entropy materials, which derive enhanced stability from a chaotic mixture of atoms rather than relying solely on the orderly atomic structure of conventional materials. After discovering high-entropy carbides in 2018, they also had to address enthalpy, which in simple terms is a measure of how sturdy each design is, while entropy is a measure of the number of possible designs that all have similar strength.
Both factors are a measure of the amount of energy and heat that end up being absorbed into the final product.
“To rapidly quantify both enthalpy and entropy, we had to calculate the energy contained within the hundreds of thousands of various combinations of ingredients that we could potentially create, instead of the ceramics we’re looking for,” Curtarolo said. “It was a mammoth undertaking.”
Besides predicting new recipes for stable, disordered ceramics, Deed also helped direct further analysis to discover their inherent properties. To find the optimal ceramics for various applications, researchers need to refine these calculations and physically test them in laboratories.
The technique is specifically tailored to a production method called hot-pressed sintering, which involves taking powdered forms of the constituent compounds and heating them in a vacuum to as high as 2,200ºC. Pressure is applied to the mixtures for as long as a few hours, with the entire process taking more than eight hours.
“The final step in synthesis, called spark plasma sintering, is an emerging method in materials science that is common in research labs,” said Professor William Fahrenholtz at Missouri University of Science and Technology, who contributed to the work.
The finished ceramics have a metallic appearance and look dark grey or black. They feel like metal alloys such as stainless steel and have a similar density, but they are much darker in appearance. Even though they appear metallic, they are hard and brittle like conventional ceramics.
Moving forward, the group expects other researchers to begin using Deed to synthesize and test the properties of new ceramic materials for various applications. Given the array of potential properties and uses, they believe it is only a matter of time before some of them enter commercial production.
“Spark plasma sintering or field assisted sintering technology is not a common technique in industry yet,” added Professor Doug Wolfe from Penn State University, who also contributed. “However, current ceramic manufacturers could pivot to making these materials by making small adjustments to existing processes and facilities.”
This research was supported by a five-year, $7.5m grant through the US Department of Defence Multidisciplinary University Research Initiative (MURI) competition, led by Professor Curtarolo and the Department of Defence High Performance Computing Modernisation Programme.
The work also included contributions from researchers at North Carolina State University and the State University of New York at Buffalo. It was published in Nature.
Want the best engineering stories delivered straight to your inbox? The Professional Engineering newsletter gives you vital updates on the most cutting-edge engineering and exciting new job opportunities. To sign up, click here.
Content published by Professional Engineering does not necessarily represent the views of the Institution of Mechanical Engineers.
Please enable JavaScript to view the comments powered by Disqus.
Download our Professional Engineering app
A weekly round-up of the most popular and topical stories featured on our website, so you won't miss anything
Subscribe to Professional Engineering newsletter
Opt into your industry sector newsletter
Please enable Javascript on your browser to view our news.
Services for home and work
Financial help and personal support
Improving the world through engineering
Flexible spaces at our head office in Westminster, London
Helping NDT professionals obtain, renew or upgrade their qualifications
Internationally recognised manufacturer of flawed specimens in the NDT and NDE industries
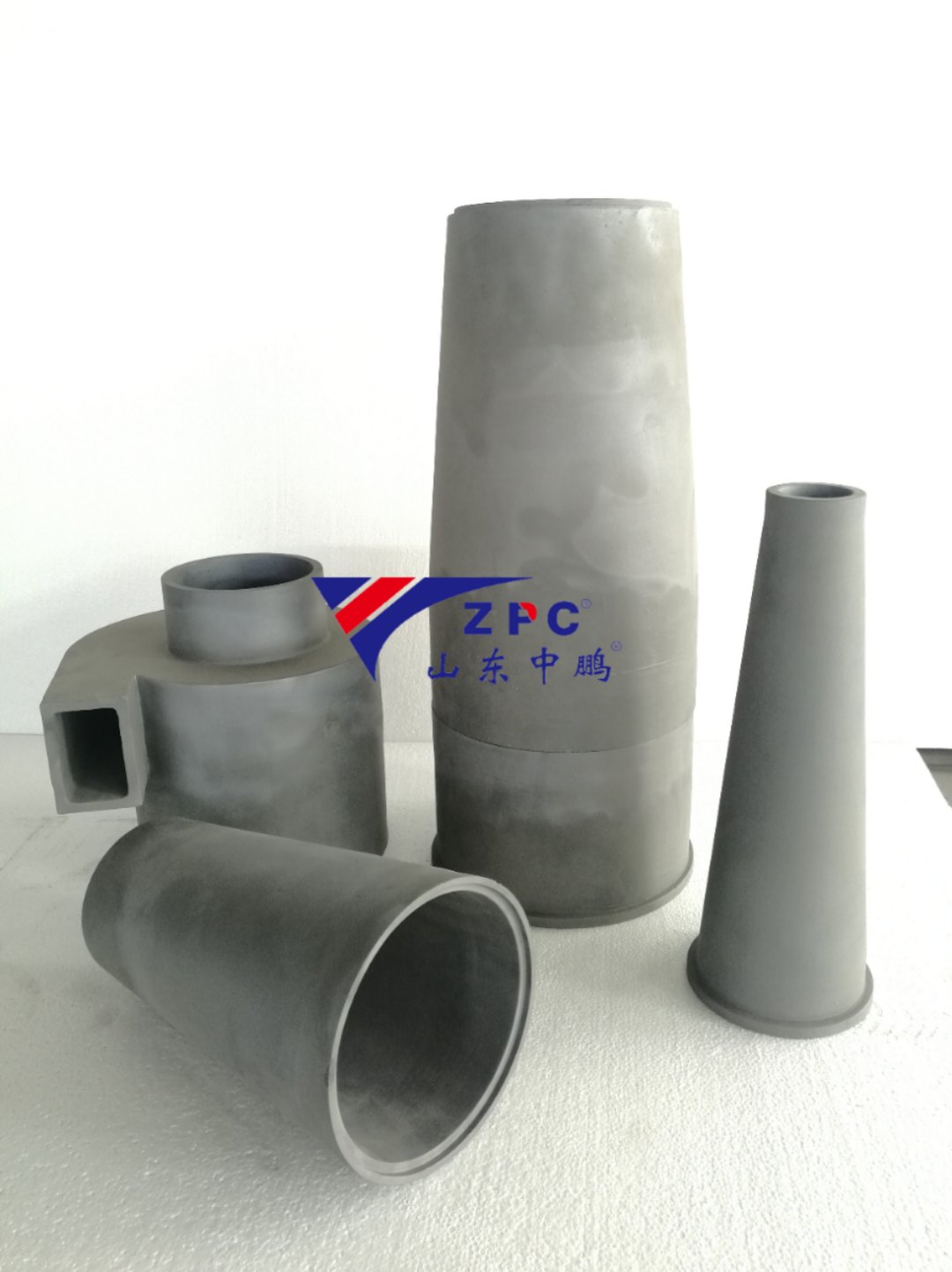
Centrifugal Cas Tube © 2024 Institution of Mechanical Engineers. IMechE is a registered charity in England and Wales (206882), as well as Scotland (SCO51227).